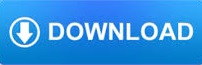
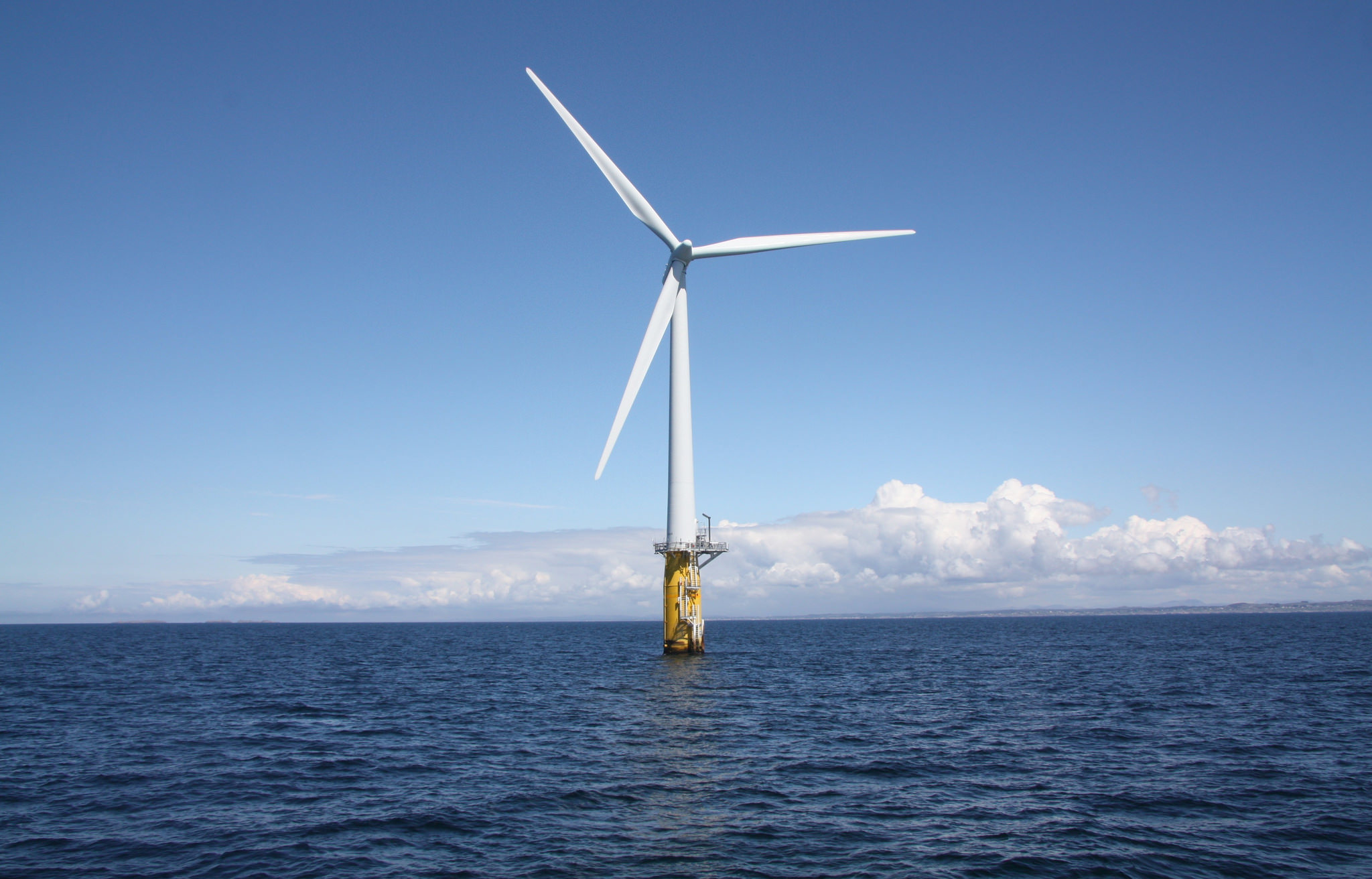
For this small-power-production case, a single wind turbine of 1- to 2-MW production capacity is considered to power the subsea equipment. The maximum power demand is 1.2 MW, 40 km from the floating production facility. Therefore, wind persistence affects only diesel storage size or tank-refilling frequency.įield 1: Small-Power Production. For short-term applications, backup diesel power generators have been considered in the study. To ensure continuous power availability, power storage or backup power generation can be considered. In an operator study, the system has been applied to an oil field that is a long tieback to existing facilities (Field 1), and an oil field combined with subsea processing with high power demand (Field 2). System Application to Subsea Field Development

Reduction or elimination, in certain specific long-tieback scenarios, of subsea power-distribution equipmentīecause hydraulic and chemical lines are among the most-burdensome components of subsea control-system distribution CAPEX, accounting for up to 80% of the cost of a subsea control umbilical, a further benefit can be achieved by equipping the floating power-generation facility with chemical-injection skids, thus reducing the length of these lines.Reduction of umbilical and cable length for subsea production and processing facilities.Reduction of required power-generation capability and footprint onboard the floating production storage and offloading (FPSO) vessel or platform.The system consists of the integration of the floating foundation with a properly sized wind-turbine generator, with all the required utilities hosted directly onboard the same floater.Ī floating power-generation facility based on a wind turbine installed in the proximity of subsea production facilities is a way to develop the following advantages for long-tieback field developments: It is designed to extend the offshore wind-energy concept from the power grid to subsea field-development application. The Windstream system that uses the previously described technology is a proprietary solution under development. The whole floating system can be anchored with three-to-six low-tension mooring lines, depending on environmental conditions. As a result, only the central cylinder is exposed to the wave energy. Because this stability is provided by weight, large hydrostatic stiffness is unnecessary. This assembly provides flotation with excellent stability thanks to the distance between the center of gravity and the center of buoyancy. The assembly of the basket and the substructure behaves as a rigid body if all tendons are loaded. The substructure is connected by tendons to a basket counterweight filled with solid ballast that provides stability with pendulum-restoring forces. This concept uses a minimal floating hexagonal tubular substructure that supports wind-turbine tower and provides necessary floatability. The operator has developed a floating substructure technology for offshore wind farms known as HexaFloat. Decarbonize the field by adopting a renewable energy sourceĬoncept Background and Potential Application.
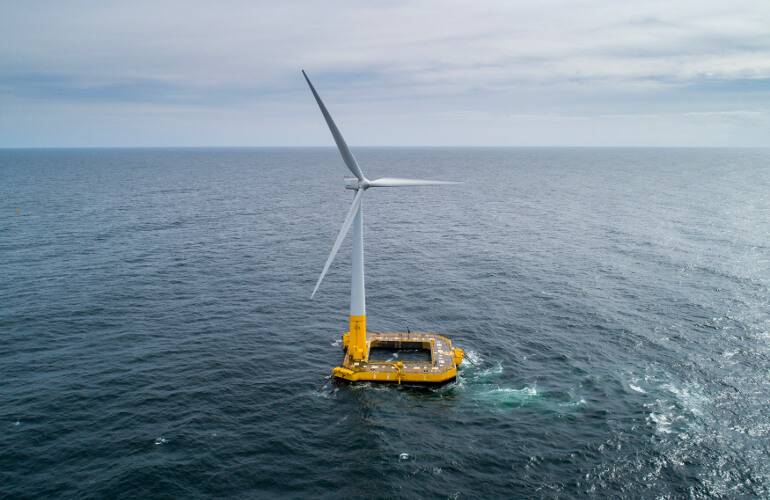
Minimize CAPEX by reducing the distance between the subsea-field production location and the topside equipment supporting this production.Saipem launched an initiative aimed at finding a solution for the management of subsea field-power demand, bearing in mind two primary considerations: The complete paper discusses a floating wind-turbine solution that is particularly cost-competitive for deepwater locations and that can unlock the possibility of deploying large wind-powered generators far from the coastline in deep water. Given this scenario, overall electric power needs may become an issue because of the extra power demand caused by the increasing number of electric consumers placed subsea. Moreover, they want to minimize new production floating facilities. Operators are moving active production and injection equipment onto the seabed with the aim of reducing capital expenditures (CAPEX) or topside space requirements.
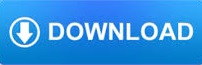